Three important tips that will improve efficiency in your warehouse.
- Efficiency versus time – how to coordinate work well?
- Improving warehouse efficiency:
- analysis of warehouse operations,
- analysis of human labour,
- reducing delays and unnecessary costs.
- Summary.
Efficiency versus time - how to coordinate work well?
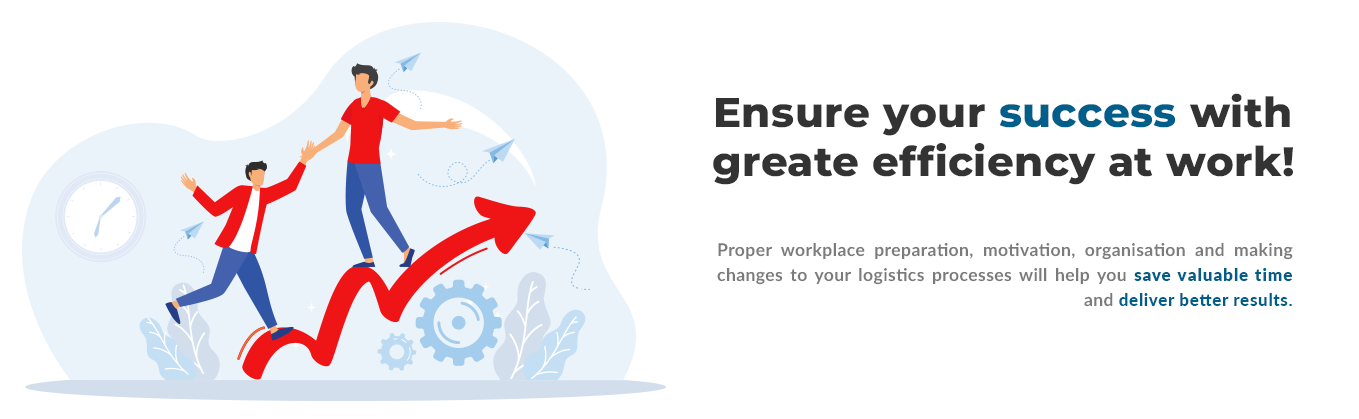
Analysing work in general terms, it should be said that productivity is a measure of a worker’s efficiency. For a more precise definition, the volume of production converted per employed person or per specific period of time – the so-called man-hour – is taken into account.
The level of productivity depends on a number of interrelated conditions:
- an appropriately prepared workstation,
- employee qualifications,
- motivation to work,
- quality of work items,
- organisation and working conditions,
- living conditions,
- relations between employees.
The same is true of working in a warehouse. Efficiency is closely linked to the time it takes to carry out all logistics processes. In order to increase it, it is necessary to analyse the activities performed and make changes to them that will lead to a noticeable reduction in time.
Improving warehouse efficiency:
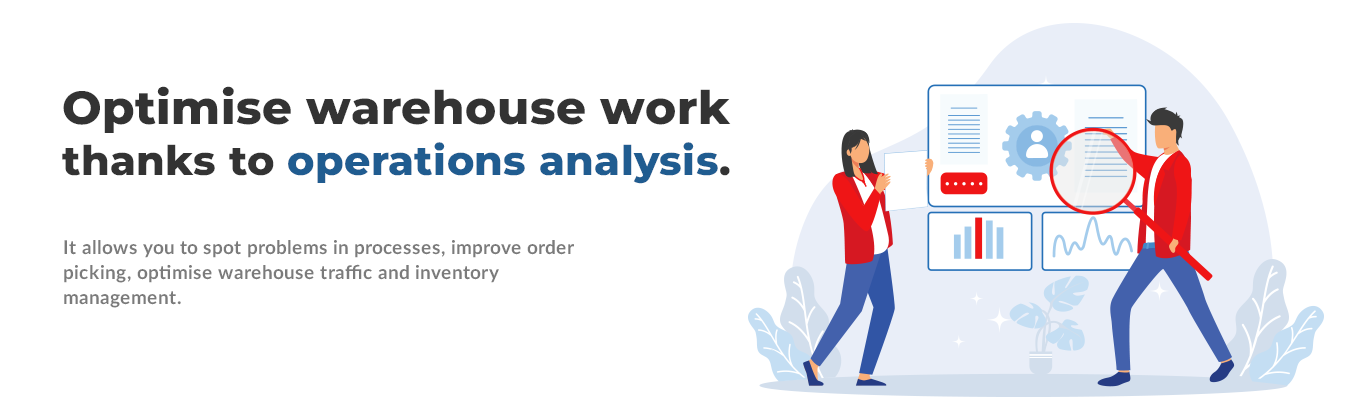
- Analysis of warehouse operations.
At the outset, it is advisable to identify the tasks that are carried out in the warehouse. All administrative tasks must be taken into account – preparation of documentation, reports, waybills, distribution of duties among employees, all meetings, etc. In many of these tasks it is possible to find elements that we are able to correct and improve accordingly.
Once we have this carried out, we focus on warehouse traffic. We check that we are not generating too many empty runs. How about focusing on wave picking, or picking by assortment? This will allow us to process several orders at a time.
We then check how the unloading and loading of goods is going. Deliveries should be on schedule, with no delays or stoppages, as this disrupts the initial plans and reduces efficiency.
With the above data, we analyse one of the main processes – order picking. This is usually the most time-consuming stage of work in the warehouse and requires a meticulous approach. It can be improved in a number of ways – from designing an ergonomic workstation to good staff training.
The need for specific changes can also be easily picked up by analysing the stock management process (storage of seasonal products, identification of loads, possible simplification of procedures).
Every mistake that is caught can be quickly corrected and almost completely eliminated.
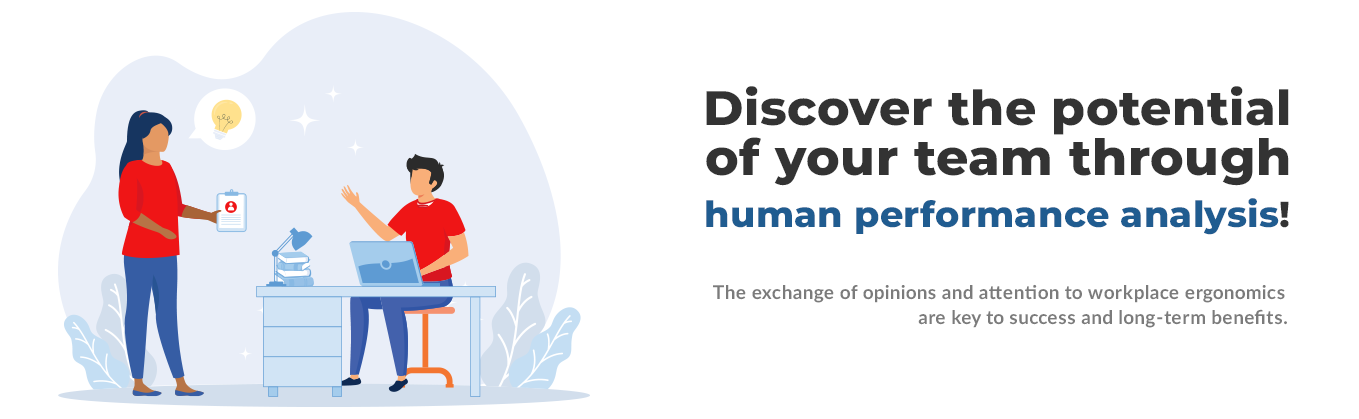
- Analysis of human labour.
Here, you can get a lot of specific information in a quick timeframe.
We start by finding out what employees think. Most often, they are the ones with valuable ideas and insights. After all, no one else will express themselves better about the type of work and possible improvements than the person who works on a particular job.
The working style and current productivity of employees can also be analysed. Some individuals may need additional training and courses.
Regular meetings and exchanges of opinions with employees also have long-term benefits. Future actions can be planned well in advance, and this can simply come in handy in the event of major twists and turns, such as the recent pandemic or global crisis.
Every workplace should also be checked for ergonomics – whether it is suitable for the people working there and the type of work being performed. Non-ergonomic workplaces have a negative impact on the physical condition of operators, causing fatigue and tiredness.
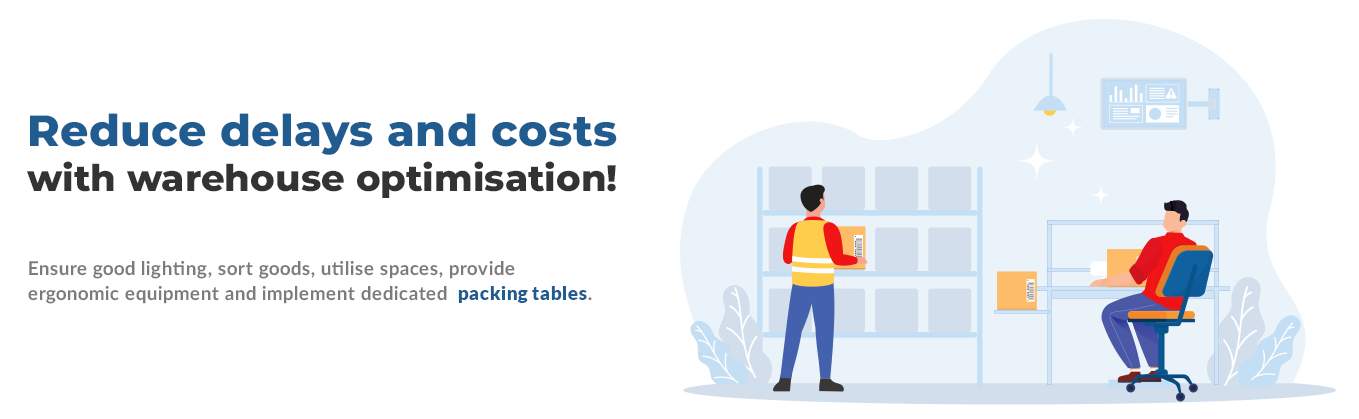
- Reducing delays and unnecessary costs.
- Generated costs. These can be reduced by making sensible savings. In any warehouse, the basis for efficient and safe work is good lighting. However, it is essential to ensure that it is energy-efficient.
- Optimising the placement of goods. It is unwise to run in different directions when picking orders. It is worth tracking orders from this angle. This will help sort the goods on the warehouse shelves accordingly – items that are most frequently purchased together can be grouped together in close proximity.
- Making the most of empty space in the warehouse. It makes no sense to keep a small amount of goods in a huge warehouse. To minimise costs, you can rent a smaller space or make extra use of the one you have. It can be advantageous to install larger, better-fitting racks, to use different stands and special platforms. You can also consider subletting unnecessary space to other businesses.
- Ergonomic equipment. This topic has already been briefly mentioned, and we cover it in detail in this article. The right equipment must be tailored to the people working at it. Ergonomics applies to tables / entire workstations, as well as to the tools and equipment the operator uses.
- Using dedicated packing tables to avoid shipping problems. Nowadays, with the boom of e-commerce, the main – most demanding and absorbing – work in warehouses takes place when picking, packing and shipping goods. These activities must be synchronised and carried out in a short space of time in order not to generate delays and to satisfy the requirements of the end customer. A great help is the use of professional parcel packing tables.
- Generated costs. These can be reduced by making sensible savings. In any warehouse, the basis for efficient and safe work is good lighting. However, it is essential to ensure that it is energy-efficient.
Summary.
- analysis of warehouse operations,
- analysis of human labour,
- reducing delays and unnecessary costs.
Featured articles:
The e-commerce market. Opportunities and threats.
Over the past decade, the e-commerce market has undergone a tremendous transformation. Initially, sellers treated this type of activity merely...
Logistics 4.0 – a Difficult Challenge or an Opportunity for Growth?
The concept of "logistics" emerged a long time ago, around the 10th century. Initially, it was used exclusively in a...
Ecology tendencies in packaging parcels.
The disruption caused by the pandemic prompted specialists to reexamine this topic. In April 2021, the Mobile Institute conducted a...
Warehouse robots as part of logistics processes.
The basis for the automation of logistics processes in the warehouse and their efficient running is both the use of...
Envelopes. Types and their use.
At first association, an envelope is a paper package used to send letters or other flat items using postal mail....
Leave a Reply